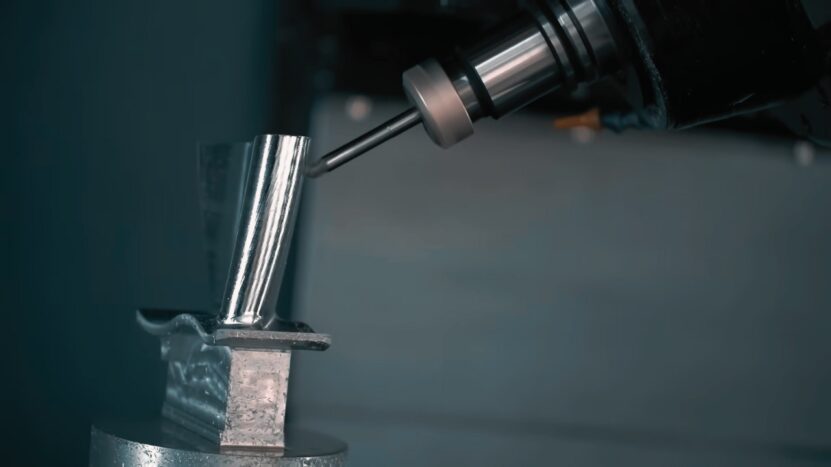
Share Post:
CNC machining has revolutionized the automotive industry and has enabled highly precise and complex custom part fabrication. If it was previously necessary to request original parts exclusively produced by the authorized factories of car brands, today, the trends are changing. On the other hand, access to car parts is also easier with the help of CNC machines.
However, effective design of these parts demands that the designer should have a deep-rooted knowledge of not only the design process but also an in-depth understanding of what CNC machining can do. These are the two key things that lead to a perfect realization without major challenges.
To guarantee that your custom car parts will meet your expectations and work as they were meant to, it is very important to watch out for common mistakes that may cause very expensive rework or even result in failure. Without errors until complete realization, and for that see what is very important to know.
Table of Contents
ToggleUnderstanding CNC Machining Limitations
Before we go into the details related to the most common mistakes, we think it is very important to familiarize you with CNC machines, what they can do, and most importantly what they cannot do. We start from here because the most common mistakes happen precisely because of the limitations, so let’s see what you need to know.
Material Selection: CNC machining is not compatible with all materials, so you should be careful when choosing. Tool steel, for example, can become a very hard material to a machine that will quickly wear on the carbide inserts. What could you choose? Opt for materials that work well with the design and that are within the capabilities of your CNC machine, because that’s the only way you won’t make a mistake and prepare something that will be successful.
Part Complexity: CNC machines are capable of producing very detailed parts, but we advise you to do them only when necessary. However, overly complex parts will increase processing time, cost, and the likelihood of producing scrap. Reduce design complexity whenever feasible without affecting functionality.
Tolerances: CNC machining can hold very tight tolerances. The ability to specify accuracy is key so do it right; otherwise, you might be asking for more precision than necessary which could increase costs.
Tooling: Whether or not adequate tooling is available can influence the feasibility and cost of your design. Check with your CNC machine operator or tooling supplier to make certain that the tools mentioned are available.
Common Design Mistakes
Underestimating Machining Time: The time needed for CNC machining is often underestimated. This is especially the case with complex parts. Consider the setup time, tool changes, and any issues that might appear, so as to work within the time limit and not delay.
Ignoring Fixture Design: The part has to be held securely during machining by a properly designed fixture to avoid errors in the production process. An ill-designed fixture will cause inaccuracies and rework.
Failure to Include Support Structures: This can result in defects and scrap by overlooking the following: For parts with overhangs or undercuts, support structures are likely needed to prevent material from breaking or chipping. The choice of cutting tools and machining parameters should be greatly influenced by the desired surface finish. Specify the required finish so that the part meets your expectations.
Wrong Parts Are Used During Service: If there is a CNC machine, it is important to do regular service. If the time comes that you need to replace any of the parts, it is most important to use quality parts so that you can continue the quality manufacture of everything you need from car parts. It is best to choose suppliers like Proleantech.com who always offer only the best parts, ideal for replacing your CNC machine.
Design Tips for Successful CNC Machining
Ensure that it is Simple: Reduce your design to the bare minimum while retaining functionality. Remove those unnecessary features or details that would make the job more expensive or time-consuming to machine. That way you will achieve the effectiveness and efficiency you need and you will easily reach the final outcome.
Keep Manufacturing Constraints in Mind: The limitations of CNC machining include tool size, spindle speed, and whether or not the delivery system can provide coolant effectively. Design your part with these constraints in mind. It’s good to know these important things to save yourself time that would be wasted if you didn’t know these small but significant limitations.
CAD Software: Make use of CAD software by creating 3D models with an accurate description of your part. 3D models are the best way to see the details and get to the final thing you need, which should come out as a finished part. Visualization and detection of possible issues are the ability it gives the user plus expressing what you need in terms that a CNC machine operator will understand.
Consult an Expert: Should you have any doubt regarding both the design and the CNC machining process, then later on do not hesitate to consult a professional engineer or CNC machine operator. From here you can see that it is important to have a professional who understands how to operate the CNC machine, but above all a professional who will find the solutions in moments of uncertainty in the production of car parts.
Prototype and Test: If your part works fine, then create a prototype to identify any design flaws or manufacturing difficulties with it. Prototypes are the best step that you should choose to make sure that actually after producing that prototype you can proceed with the production of the final part. Test the prototype to confirm that it meets your functional requirements and performance expectations.
Conclusion
However, by not making these common mistakes and following these design tips, you can increase the chances of successful CNC machining and make custom car parts that are above and beyond what you expected. Keep in mind, that it all comes down to care in planning and precision to realize optimum results when designing and manufacturing custom automotive components.
Related Posts:
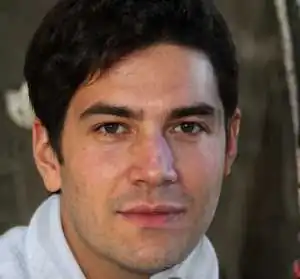